|
1996年,多位富有遠見的人才共同創立了Epistar,並昭告LED時代的來臨,數十年後的今日,固態照明不僅已進入大眾市場,更擁有無窮的潛力和希望。Epistar不斷創新、突破與深入的洞察,成為磊晶的創新設計生產者,並以日積月累的專業知識和全方位的能力穩坐世界LED供應商的龍頭寶座,同時與聲譽卓著的世界品牌,協力推廣手機螢幕、筆電和電視等領域的LED應用技術,努力創造日常固態照明的優勢。
EPISTAR秉持以一貫的初衷,展現智慧營造良好的「客戶-供應商」關係。EPISTAR始終相信,在互助共生、緊密交織的LED產業中,唯有與客戶密切合作,方能創造出雙贏加乘的佳績。基於此Epistar設計出獨有的「Co-activation Service」服務模式,與客戶協同設計開發提升產品性能,解決工程端與應用問題,並追求完美的品質控管水準。透過「Co-activation Service」緊密的合作關係,精確評估下游企業和消費者的多元需求,協助所有Epistar客戶服務其客戶時,也獲得最佳的客戶滿意度。
EPISTAR位於推動LED科技應用商業化,引領全球邁向固態照明時代的關鍵地位。展望當下,LED時代已經拉開序幕,EPISTAR也正以前所未有的方式茁壯成長,迎接各項挑戰,努力實現LED應用無限可能,將更好的光源帶入日常生活中。
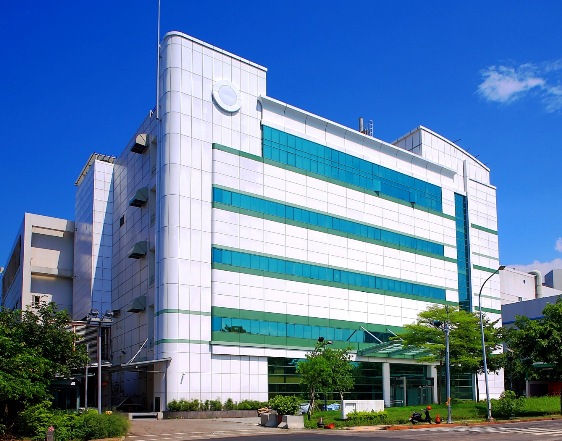
|
|
▲TOP
|
|
過往最適處理NH3之廢氣流程為使用濕式洗滌塔作為第一級前處理,並透過整廠之大型濕式洗滌塔作為二次處理後排放大氣,已達環境排放要求。過程中產生大量含氨氮之廢水,經由酸鹼中和調勻後排放納管,因此分別產生高濃度之含氨氮廢水。
另外於製程流程中也使用部分含氨之化學品(ex. NH4OH,NH4F),故該化學品之分流與後續處理必須被關注。以整體LED廠區之總氮分佈,約97 %之總氮貢獻為氨氮與有機氮,約莫3 %為硝酸鹽氮。故可以很清楚的去設定應投入削減或因應之對象為磊晶製程。
當確認待處理或削減之對象後,考量投入、處理、產出之不同面向,以不同的處理途徑所衍生或因注意的空水廢各項產出,實有多方考量之必要。
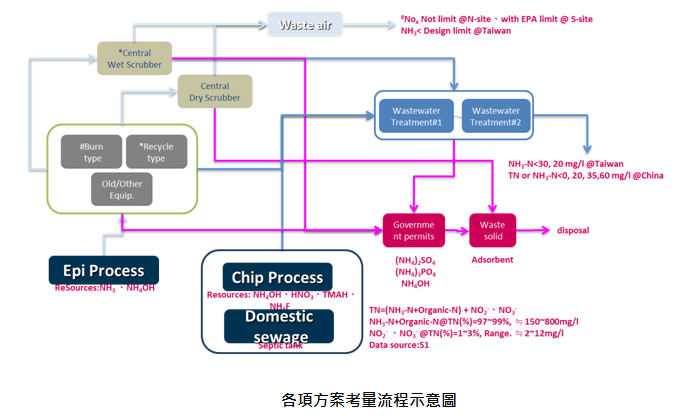
透過供應鏈的建立,與政府建立三方合作逐步建立再利用流程並產出可再利用之資源並回到供應商處,以實現增加產品生命週期並進而增加企業競爭力,當然除了資源再利用以外也將我方之廢棄物轉成其他工業鏈之原始材料,這十足就可以說是”搖籃到搖籃”的一個新契機,不過還是有部分廢棄物還是得透過焚燒及掩埋方式安定化,所以我們稱為該流程為一個“永續圈”適當呼應了”循環經濟”的理念。
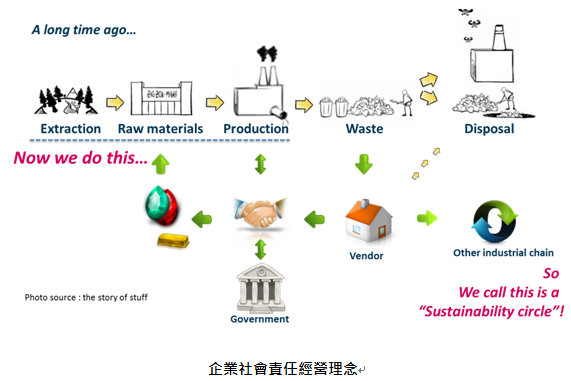
|
|
▲TOP
|
1. |
含氨氮廢水之分流狀況 |
|
磊晶MOCVD生產機台所排放之氨氣會至N/S洗滌塔,N/S所洗滌下的氨水會存放至原水TANK(濃度約為6 %)先暫儲存,會將此原水持續注入至氣提塔進行氨水提濃,提濃後的氨水(約28 %~30 %)則會進回收氨水TANK佔存之委外清運。
另含氨氮之化學品使用(ex. NH4OH,NH4F),目前採廢液收集後委外處理或個案再利用,同樣做好分流且資源化。該流程與許可均已於103.11年完成取得。
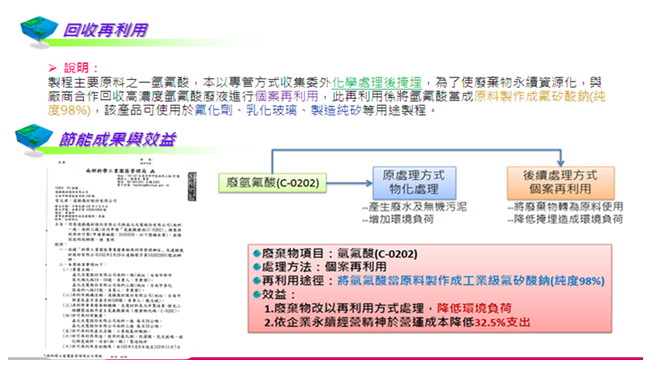
|
2. |
減量措施、投資及額度 |
|
整套減量措施進行如下描述: |
(1) |
經過前段處理完的含氨廢水,經過熱交換器與氣提塔塔底的液體熱交換後(約25度→約85度)進到氣提塔內部。 |
(2) |
進到氣提塔後,大部分的NH3蒸發至塔頂此時含氨氣體會透過冷凝器冷凝回收。 |
(3) |
經過熱交換後的含氨氣體則冷凝後收集在桶槽。 |
(4) |
未冷凝的含氨氣體則由桶槽揮發到吸收器,而透過純水將此含氨氣體吸收回收出25 %~29 %濃度氨水。 |
(5) |
塔底出來的為已去除NH3之處理後排水,此時NH3-N濃度已達30 ppm以下。 |
(6) |
處理過排水經過熱交換器與含氨廢水熱交換後達到冷卻效果,排至下一個單元(放流處or回流到N/S)。
|
|
3. |
減量前/後排放濃度、穩定度及成果 |
|
針對減量措施投入前後之放流水氨氮濃度成效進行如下說明,未導入氨氮回收系統的放流水氨氮濃度為1,030 ppm,於9/20/14導入氨氮回收系統後的放流水排放量為15 ppm以下。
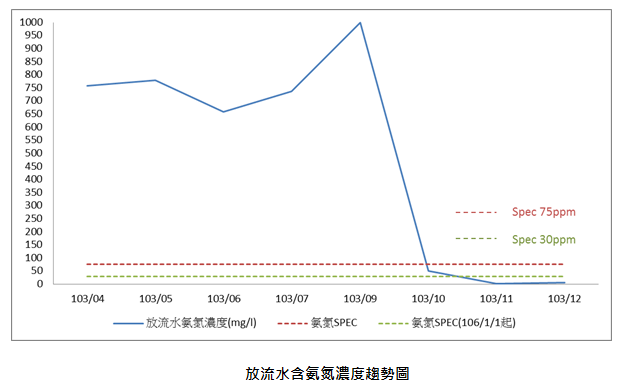
|
4. |
相關設施查驗、管理及運作情形 |
|
系統要妥善且穩定之運轉,過程中設施之查驗保養與應變管理,亦屬重要。故分就日常保養、監控系統、維護保養與應變措施等要項簡要說明如下: |
(1) |
以日常保養為例,利用實場抄表確認運轉數據符合設計與環境法規許可之限值,並輔以人性且及時之監控系統設計進行即時監督與因應。 |
(2) |
另因應可能發生之系統風險,也規劃緊急備機切換運轉機制,以確保廠區營運與工安環保無虞。並增設多項實地且有效應變偵測與防災措施設備。 |
為了讓該技術與理念,所投入之減量技術與相應衍生物之清理,故分別也投入大量的人力資源進行技術外部溝通與許可取得,並於2014年已陸續將其設備導入至相關製程廠區,目前其廠區放流水氨氮濃度皆已符合園區納管標準,且放流水氨氮濃度皆低於30 ppm。
|
產製氨水於2013年經由南部科學工業園區管理局協助與支持,正式通過取得台灣第一個氨水個案再利用核備。2013年底正式以再利用方式將其氨水清運至再利用機構進行再利用。2014年經由本成功案例目前也順利於各廠區申請通過氨水個案再利用核備。
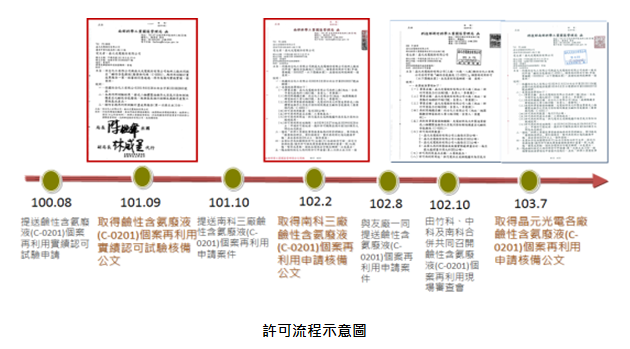
|
相應含氨廢氣回收設備與衍生物效益說明如下: |
(1) |
氨水回收濃度與重金屬離子成份皆能符合CNS工業級氨水標準。2014年度晶電相關廠區之氨水實際回收量達2,009(公噸)。預估2015年可以產生5,760(公噸)氨水。 |
(2) |
晶電相關廠區節水方面,每廠區約180(m3/日),以安裝四廠區計算每月用水量可以節省約21,600(m3/月)。預估每年節水259,200(m3/年)。 |
(3) |
以廢水排放而言,晶電相關每廠區約180(m3/日),以安裝四廠區計算每月廢水量可以減少約21,600(m3/月)。預估每年減少廢水排放259,200(m3/年)。 |
氨氮廢水管理因應過程中,整個產官學界均針對各項可能技術、國內外因應經驗等展開多項之交流與分享,晶元光電過程中也利用多次基會於公開場合分享經驗與經歷。Ex. 2012.11.20於南科管理局主辦之廢水處理技術研討會、2013.04.09於台灣光電半導體協會TOSIA環保暨安全衛生永續委員會分享”高科技LED產業氨氮廢水回收處理實務經驗分享”、2014.09 SEMICON Taipei_ Sustainable Manufacturing Gallery分享”LED產業的氨管理衝擊及契機”。
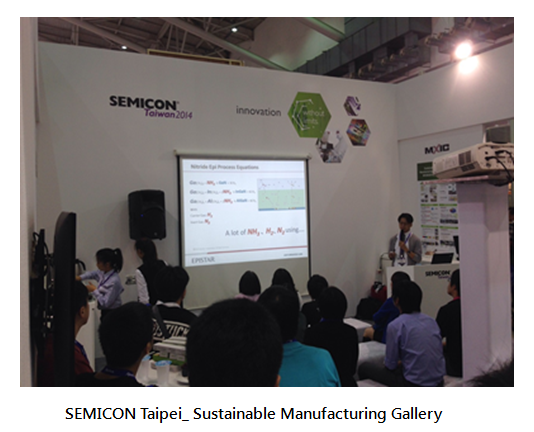
|
|
5. |
特殊績效或卓越事蹟 |
|
氨水回收設備氣提塔熱回收:節省瓦斯量20,304 Nm3/年、節省費用43萬元/年及減少二氧化碳排放量49公噸/年。
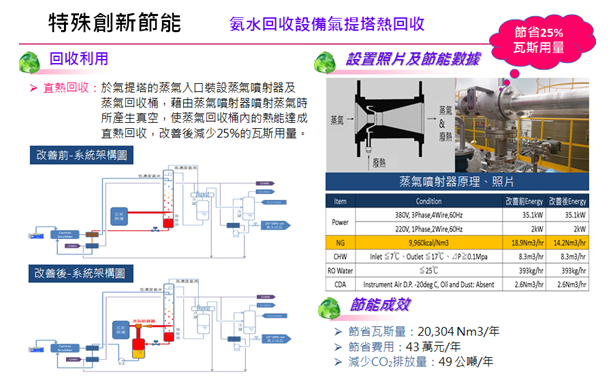
|
|
▲TOP |
|
現階段已朝向”零排放零污染”之目標進行著手規劃,將濃度25 %~30 %氨水提出蒸餾(油分)、純化等步驟產生GNH3(5N)後填充至鋼瓶後,經BSGS系統供氣至MOCVD機台使用,預計回收效益為37,488,000元/年。
|
|
▲TOP |
|